Kanban metrics
Learn how key Kanban metrics can streamline your process and boost productivity, giving your team the competitive edge they need.

Understanding Kanban metrics
Kanban, a term which hails from the Japanese word for ‘visual signal’, represents a method of visualising work. Kanban enables teams to manage their workflow more effectively and efficiently. Key to a successful Kanban system is the use of metrics, which offer insights into a team’s performance and provide a data-driven approach to continuous improvement.
In this article, we will explore the most important Kanban metrics, how they’re measured, and why they matter. Understanding these metrics is not just about measuring progress; it’s about creating a culture of transparency and continuous improvement.
The basics of Kanban
Kanban is a strategy to optimise the flow of work. Kanban helps teams focus on the completion of tasks by using a Kanban board that provides a visual representation of work at various stages. Each column on the board represents a different phase of the workflow, allowing teams to identify bottlenecks and understand their system’s capabilities. There are lots of different examples of Kanban boards you can choose for your workflow. You can even use Kanban for your personal workflow.
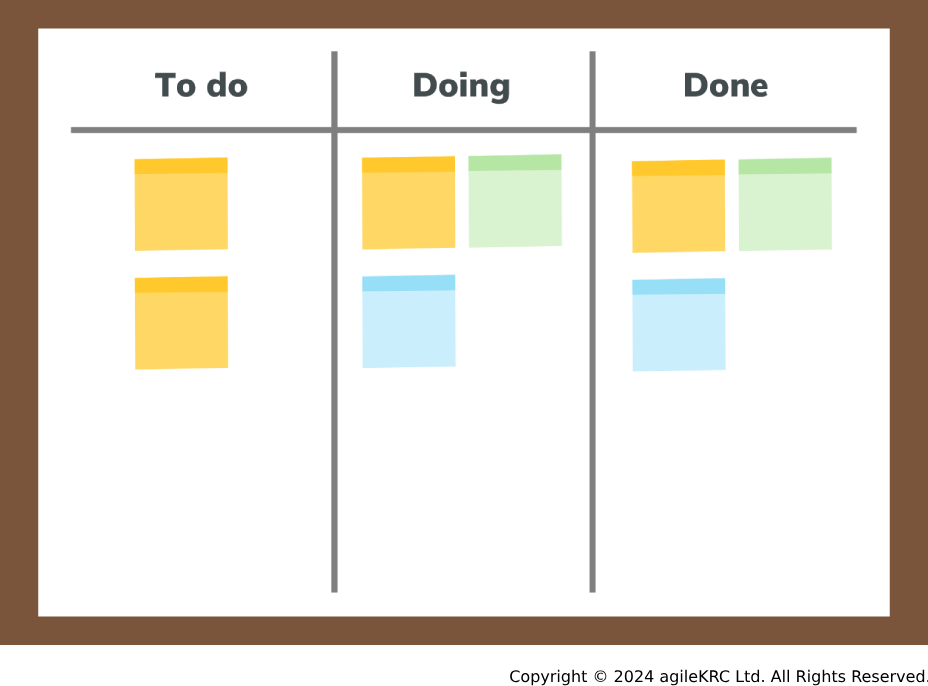
Adopting Kanban involves creating a workflow that reflects the actual process, establishing a pull system that prevents overloading team members, and using visual cues to highlight the status of different tasks. By focusing on the work in progress and prioritising tasks, teams can reduce cycle time and improve delivery rates, which are key outcomes for Agile performance.
Kanban metrics are the tools that offer teams the power to make informed decisions, streamline processes, and ultimately deliver better results to customers.
Key Kanban metrics
Lead time
Lead time measures the duration from when a task is first requested to when it is fully completed. It tracks the time a work item spends in the entire Kanban process, including both active work periods and wait times.
Understanding lead time is vital because it directly impacts customer satisfaction. Shorter lead times typically result in happier customers, as they do not have to wait as long for their requests to be fulfilled.
How to calculate lead time
To calculate lead time, record the date and time when work on an item is started (requested) and when it is completed. Subtract the start date/time from the completion date/time.
How to improve lead time
To improve lead time, analyse and eliminate unnecessary steps in the workflow, automate processes where possible, and manage work in progress to avoid bottlenecks.

Cycle time
Cycle time is the actual time spent working on a task until it reaches completion, not including periods where the task was on hold or in a queue. It is a subset of lead time, starting from when work begins and ending when it is delivered.
Cycle time is important because it provides insight into the efficiency of the workflow process. Shorter cycle times indicate a more productive system, leading to quicker deliveries.
How to calculate cycle time
Calculate cycle time by taking the date/time when an item enters the ‘work in progress’ state and subtracting it from the date/time it is marked as ‘done’.
How to improve cycle time
Optimise the process by removing non-value-adding activities, evenly distributing workloads, providing team development, and reducing interruptions to maintain focus on the tasks.

Throughput
Throughput refers to the number of work items completed in a given period. It’s a performance metric that shows the amount of work a team can deliver in a specific timeframe.
Throughput is a crucial metric for predicting future performance and planning. A consistent or increasing throughput suggests that a team is working efficiently and is capable of taking on a certain workload.
How to calculate throughput
To calculate throughput, count the number of work items completed within a set period such as a day, week, or month.
How to improve throughput
To improve throughput, prioritise work, remove bottlenecks, automate repetitive tasks, and ensure the team has the necessary resources to complete their work efficiently.

Work in Progress (WIP)
Work in Progress refers to the number of tasks that are currently underway. It offers a real-time view of the team’s immediate workload and helps manage the flow of tasks.
Maintaining an optimal level of tasks in progress is essential for ensuring a balanced workflow. Having too many tasks in progress can lead to bottlenecks and decreased productivity, while too few may indicate underutilisation of resources.
How to calculate WIP
Calculate it by simply counting the number of tasks that are in the ‘work in progress’ stage at any given time.
How to improve WIP
To improve task levels in progress, implement limits to prevent overloading the team, monitor the workflow for potential bottlenecks, and adjust the process as necessary to ensure smooth task progression.

Cumulative flow diagram (CFD)
A cumulative flow diagram is a visual representation of work items in various stages of the process over time. It provides insights into the stability and efficiency of the workflow.
The CFD is important as it helps identify bottlenecks, work in progress, and any potential problems in the process. It also helps in understanding how work is progressing over time and whether the process is stable.
How to create a CFD
To create a CFD, plot a line graph with time on the horizontal axis and the cumulative number of tasks on the vertical axis, stacking areas to represent different stages of work.
How to use a CFD to improve workflow
Analyse the CFD for any widening gaps or areas that denote bottlenecks and address the underlying issues. Ensure stages are well-defined and resources are allocated appropriately.

Blocker clustering
Blocker clustering is the analysis of impediments that prevent tasks from moving forward in the workflow. Identifying common reasons for blocking can lead to process improvements.
Understanding blocker clustering is important as it helps to identify and address systematic issues that can cause significant delays, thus improving overall workflow efficiency.
How to identify blocker clustering
Identify blocker clustering by categorising blocked items and looking for patterns or frequent occurrences of similar blockages over a set time period.
How to mitigate blocker clustering
To mitigate blocker clustering, analyse the causes of blockages, develop strategies to prevent common issues, and create contingency plans for quick resolution when they occur.

Flow efficiency
Flow efficiency measures the ratio of active work time (value-added time) to total lead time, expressed as a percentage. It distinguishes productive time from waiting or idle time.
Flow efficiency is a powerful indicator of process effectiveness. High flow efficiency means that a work item spends most of its time being actively worked on, which implies a lean process.
How to calculate flow efficiency
Calculate flow efficiency by dividing the total active work time by the total lead time for a task, then multiply by 100 to get a percentage.
How to improve flow efficiency
Improving flow efficiency can be achieved by minimising non-value-adding activities, streamlining handoffs between team members, and reducing wait times in the process.

Work item age
Work item age is the time that has elapsed since a work item has started but not yet been completed. It can be an indicator of potential delays.
Monitoring work item age is important for ensuring that items do not stagnate and that the workflow remains consistent. Older items might indicate blockages or inefficiencies.
How to calculate work item age
To calculate the age of a work item, subtract the start date from the current date.
How to reduce work item age
To reduce work item age, regularly review ageing items, prioritise them, and address any impediments to progress.

Arrival rate
The arrival rate is the frequency at which new tasks are added to the workflow. It’s an essential metric for understanding the demand placed on the team.
Knowing the arrival rate is important for capacity planning and ensuring the workload is manageable and aligned with the team’s throughput capabilities.
How to calculate arrival rate
Calculate the arrival rate by counting the number of items entering the workflow within a given time period.
How to manage arrival rate
To manage the arrival rate effectively, balance incoming work with the team’s capacity and set expectations with stakeholders regarding feasible delivery timelines.

Defect rate
The defect rate is the proportion of work items that have been identified as defective or that haven’t met the quality standards relative to the total items completed.
Maintaining a low defect rate is important as it ensures a high level of quality in the output, which contributes to customer satisfaction and reduces rework.
How to calculate defect rate
Calculate the defect rate by dividing the number of defective items by the total number of items produced in a given period and then multiplying by 100 to get a percentage.
How to reduce defect rate
To reduce the defect rate, implement thorough testing processes, encourage peer reviews, and invest in team development to minimise errors.

Tools for tracking metrics
Kanban software tools like Jira, Kanbanize, and Trello offer extensive tracking features tailored for Kanban. They provide visual dashboards, cumulative flow diagrams, and lead time distributions that articulate the health of a team’s process at a glance. Such tools often incorporate predictive analytics, offering forecasts based on current data to aid in capacity planning and bottleneck prevention.
The integration of these tools into daily operations allows teams to transition from reactive to proactive workflow management. By doing so, teams not only boost their immediate output but also fortify their processes against future challenges, ensuring sustainable growth and adaptability.
Kanban metrics best practices
Integrating Kanban metrics into an organisation’s workflow demands diligence and a strategic approach to ensure their successful adoption and the realisation of continuous improvements. Adhering to best practices, such as careful planning, consistent development, and regular review cycles, is essential for any team aspiring to enhance its operational efficiency through Kanban.
Starting with Kanban metrics
When beginning with Kanban metrics, it’s important to first cultivate a solid understanding of the methodology within the team, including defining some of the key metrics discussed in this article.
Establishing a supportive environment for these metrics involves setting clear expectations, providing the necessary tools, and ensuring that all team members receive comprehensive development.
Sustaining improvements
To maintain the benefits acquired from implementing Kanban metrics, it’s vital to embed them into the fabric of the team’s daily routines. This can be achieved through regular meetings to discuss metric trends, celebrate successes, and identify areas for further improvement.
It’s also crucial to revisit and adjust the metrics themselves as the team evolves and business goals change. Encouraging an environment of open feedback where team members can voice concerns and suggest improvements helps in fostering a culture of continuous development. This dynamic approach ensures that Kanban metrics remain relevant and continue to drive process enhancements and value delivery over time.
Infographic
agileKRC has helped shape agile thinking by leading the teams that developed AgilePM® and PRINCE2 Agile®. We take a practical, success-oriented approach. We begin by taking the time to listen and understand your needs, before offering our real-world experience and expert guidance.